Processing Technology of Shaft Forgings
The forging methods of shaft forgings can be divided into free forging, upsetting, extruding, die forging, closed test die forging and closed test upsetting according to the movement method of the blank.
In free forging, impact force or working pressure is used to make metal materials form between the front and rear two buttresses (anvil blocks) to obtain shaft forgings. The key is manual forging and mechanical equipment forging. Die forging is also divided into open die forging and closed test die forging. The metal material blank is deformed by force in the forging die chamber with a certain shape to obtain shaft forgings. It can also be divided into cold extrusion, roll forging, axial forging and extrusion.
According to deformation temperature, forging can be divided into hot forging (forging temperature is higher than the recrystallization temperature of billet metal), warm forging (forging temperature is lower than the recrystallization temperature of metal) and cold forging (at normal temperature). The recrystallization temperature of steel is about 460 ℃, but 800 ℃ is widely used as the dividing line, and hot forging is used for the steel above 800 ℃; It is called warm forging or semi hot forging at 300~800 ℃.
When manufacturing shaft forgings, in addition to ensuring the required shape and size, it is also necessary to meet the performance requirements pointed out during the use of the parts, which mainly include: strength index, plastic deformation index value, fracture toughness, fatigue ductility and resistance to intergranular corrosion. For parts working at high temperature, there are also continuous high temperature instant stretching performance, long-term performance Stress relaxation resistance and thermal fatigue resistance. The performance of large and medium shaft forgings lies in their organization and structure (hereinafter referred to as organization).
The performance of shaft forgings with different raw materials or different conditions of the same data is different, which is ultimately determined by their organization. The structure of metal is related to the composition of data, smelting plant mode, pressure processing process and technology.
Among them, the pressure processing process has a key influence on the structure of shaft forgings, especially for those raw materials that do not have isomeric changes in the heating and cooling processes, such as eutectoid and metallographic heat-resistant stainless steel, heat-resistant alloys, aluminum alloy profiles and die cast aluminum. The key is to improve the structure and enhance the performance of shaft forgings by properly manipulating the thermal process parameters during the pressure processing. The selection of pressure processing method can also improve the surface condition of the part and create the surface prestress tension stress, so as to improve the application performance of the part.
Shaft forging is also a kind of commonly used forging. The key content of this article is the corresponding standard of shaft forging heating processing technology.
Shaft type large forgings are generally used to rotate shafts. They are the core components of mechanical equipment and the basic parts of important equipment for production and manufacturing. The quality requirements are very strict. The processing process of large shaft forgings is heating before forging, forging and heat treatment after forging. Because the production and manufacture of large and medium-sized forgings are mostly made of loose parts, the damage of forgings will cause great property losses and lead to delay in the construction period. Therefore, it is necessary to formulate effective heating standards to ensure the safety of ingot heating, and reduce the heating time to exceed the resource saving.
When charging at indoor temperature, the heating capacity of the heating furnace can be used for the heating of steel ingots. According to the simulation, the ground stress and temperature field of ingot during heating are obtained. The geostress in the ingot core is a three direction tensile stress, and the radial geostress is the largest. The maximum values of radial geostress and surface center temperature difference occur during the bottom temperature period and the phase transformation period of the ingot core. From the aspect of rapid heating, the main parameters for the improvement of heating standard are that the insulation temperature of rudder stock ingot during the phase transformation period is 850 ℃, the insulation time during the phase transformation period is 1 hour, and the calcination insulation temperature is 1235 ℃; The thermal insulation temperature of aircraft propeller shaft ingot during phase transformation is 850 ℃, the thermal insulation duration during phase transformation is 0.8 hours, and the thermal insulation temperature during calcination is 1220 ℃.
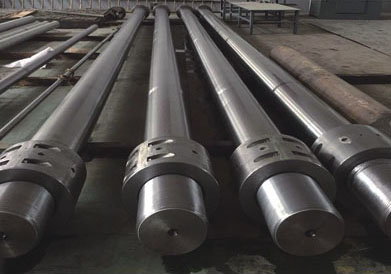